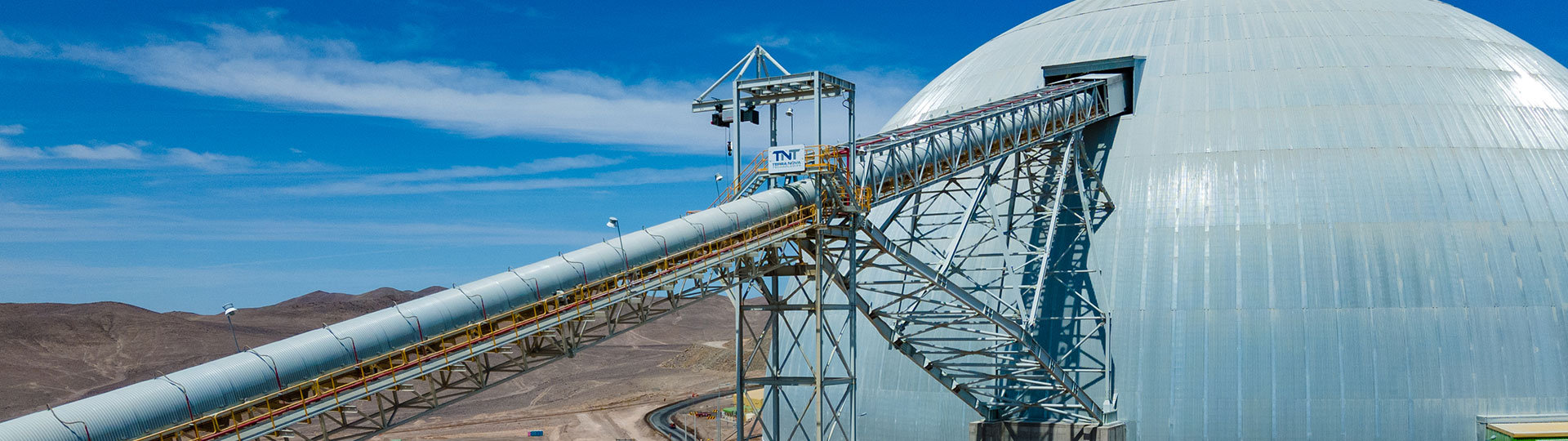
Equipment & Systems
Materials handling systems that go the distance
TNT’s mining material handling equipment and systems are dependable, high quality and built to last. Utilizing state-of-the-art technology, our expertly engineered systems are designed with the guarantee of high performance and suitability for a wide range of mining industry applications.
Our proprietary patented Super Portable® mobile equipment and custom stacking systems are synonymous with high-capacity multi-lift heap leach stacking systems throughout the mining industry. The Super Portable® systems have been adapted successfully into dry tails stacking solutions, in-pit crushing and conveying (IPCC) systems, as well as high-capacity waste stacking solutions utilized in overburden and waste rock applications.
At TNT, we take a unique collaborative approach to our projects, with early contractor involvement in developing tailored mobile stacking, conveying and crushing solutions to suit our client’s requirements. This allows us to optimize both CAPEX and OPEX, delivering projects on time with innovative technical solutions that prioritize safety, reliability and productivity in underground and open pit mining applications.